After seeing some of the threads on here I thought I have a go at anodising so I made myself a little production line and this is the result...
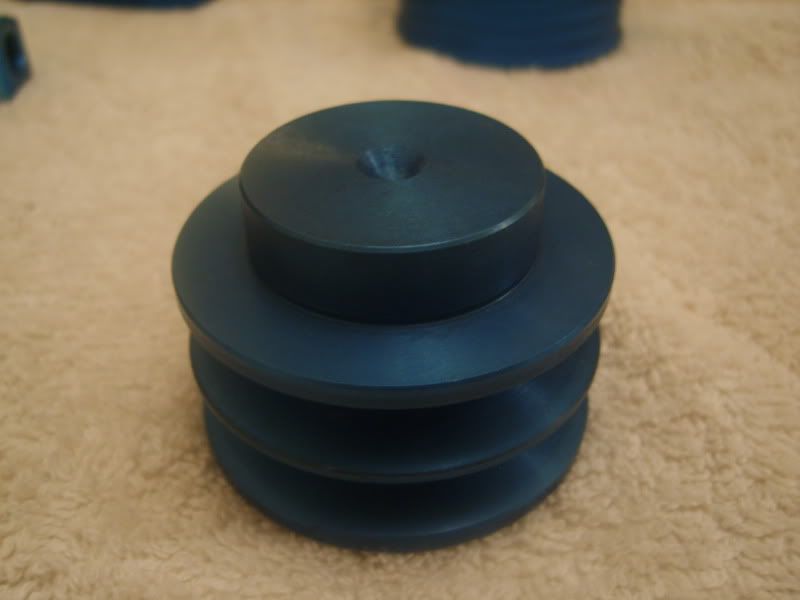
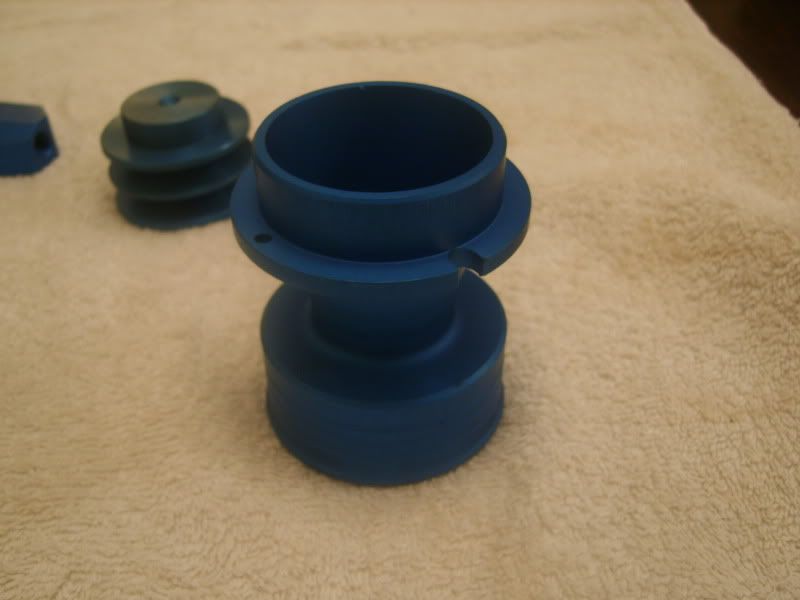
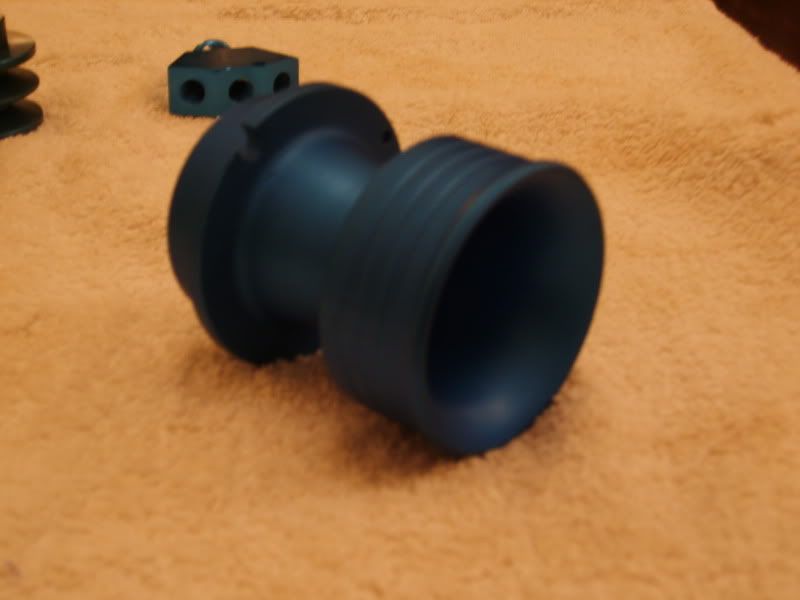
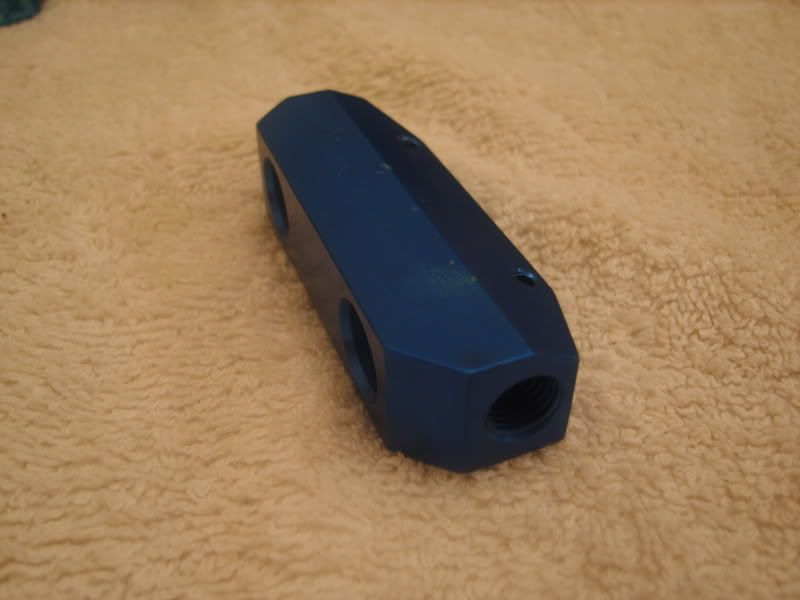
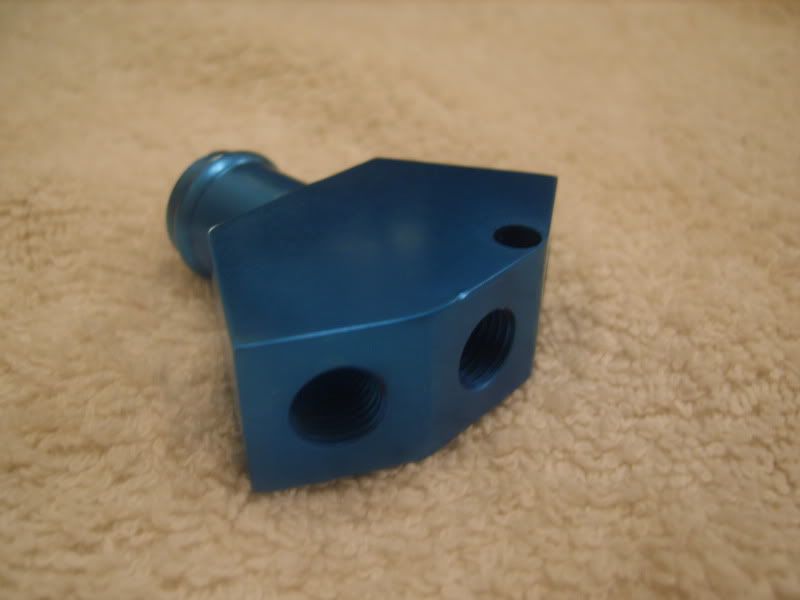
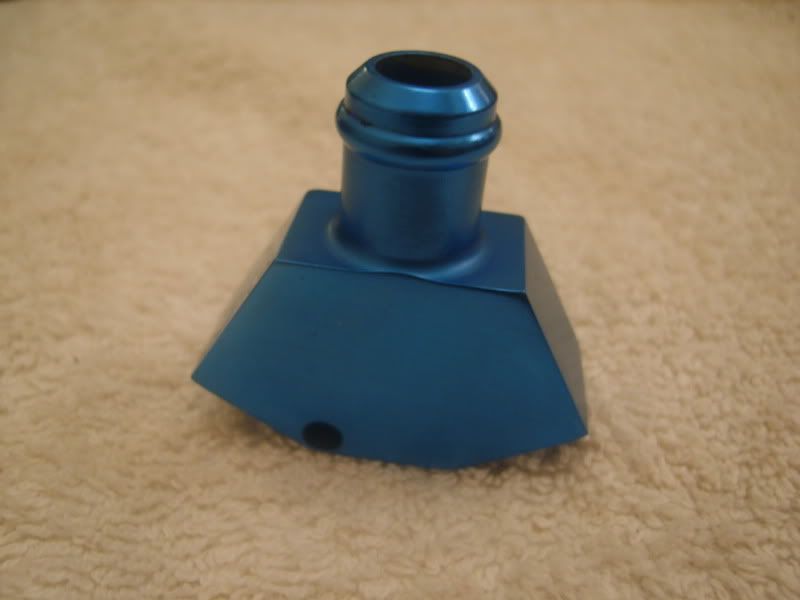
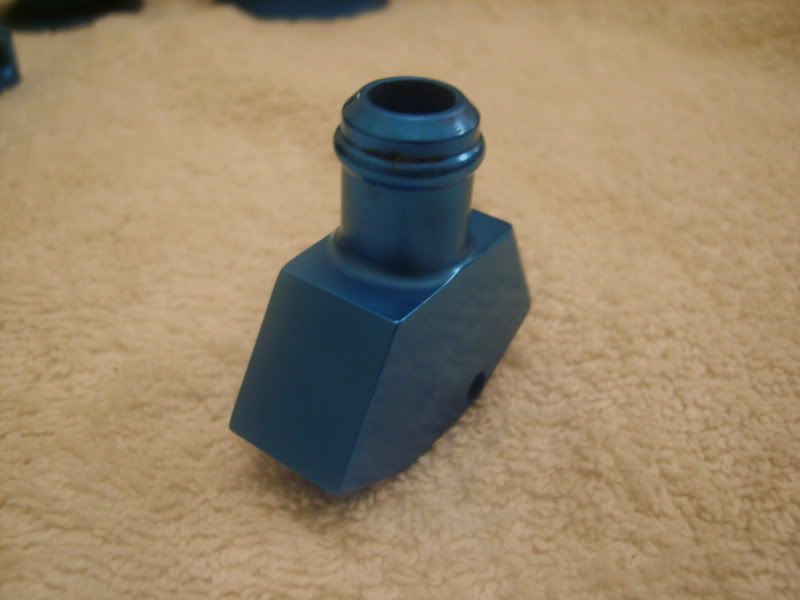
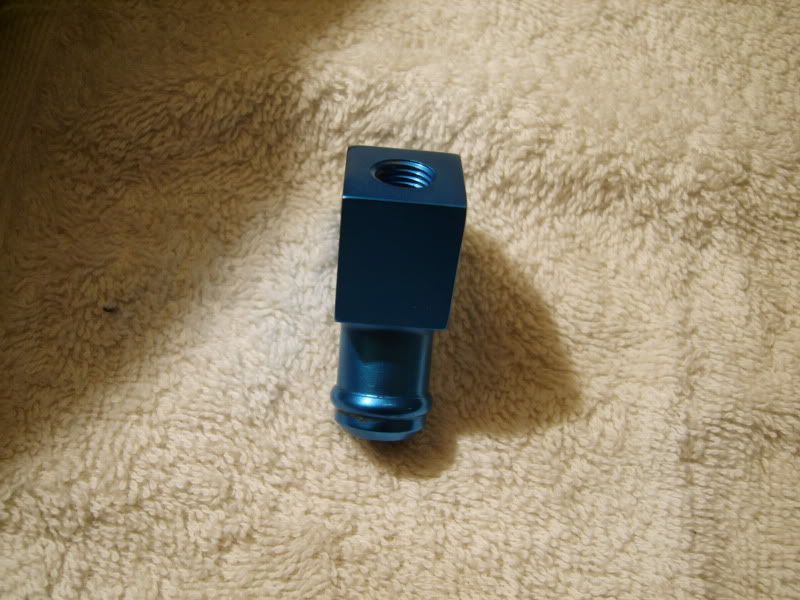
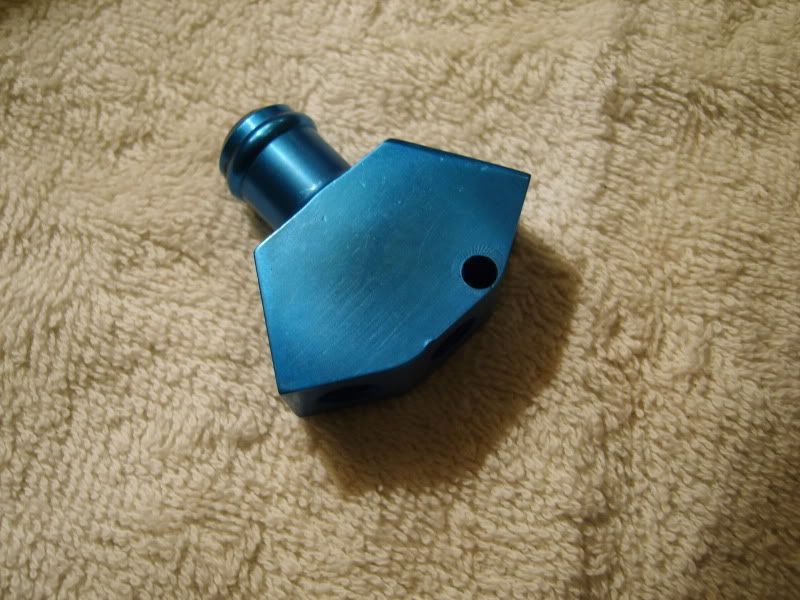
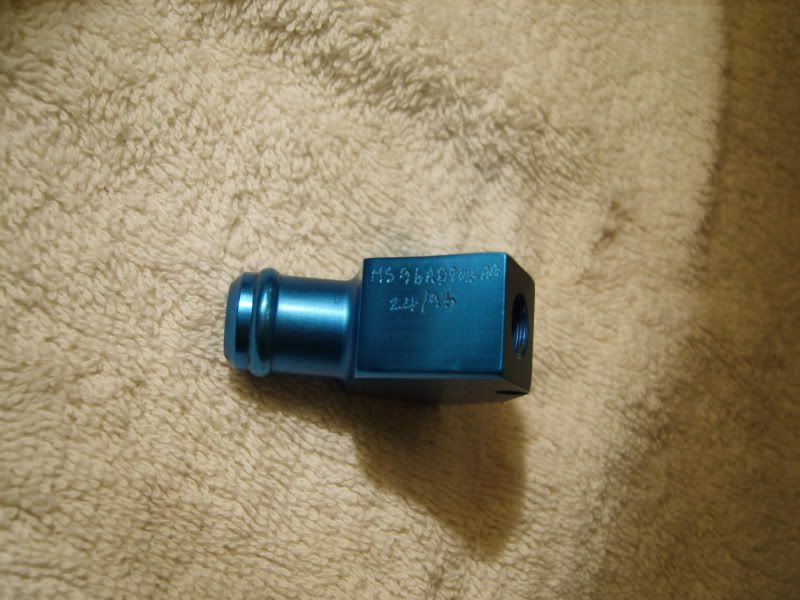
Only got blue dye at the minute but I have some gold and red arriving this week...
Some of the parts need to go back in, but overall i'm quite pleased...
Ian
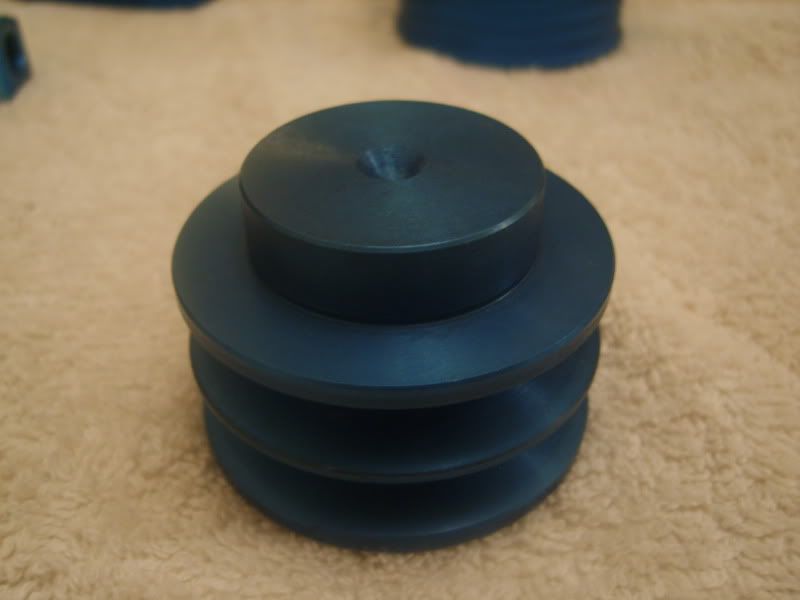
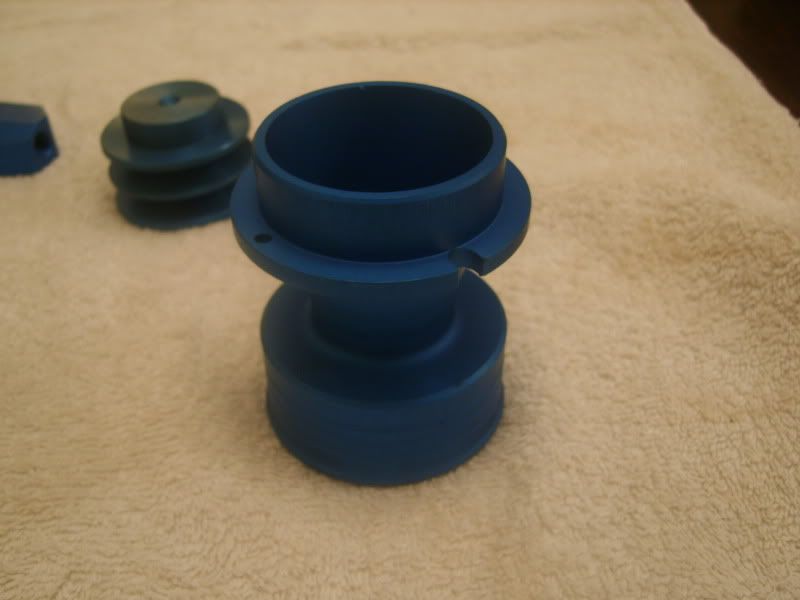
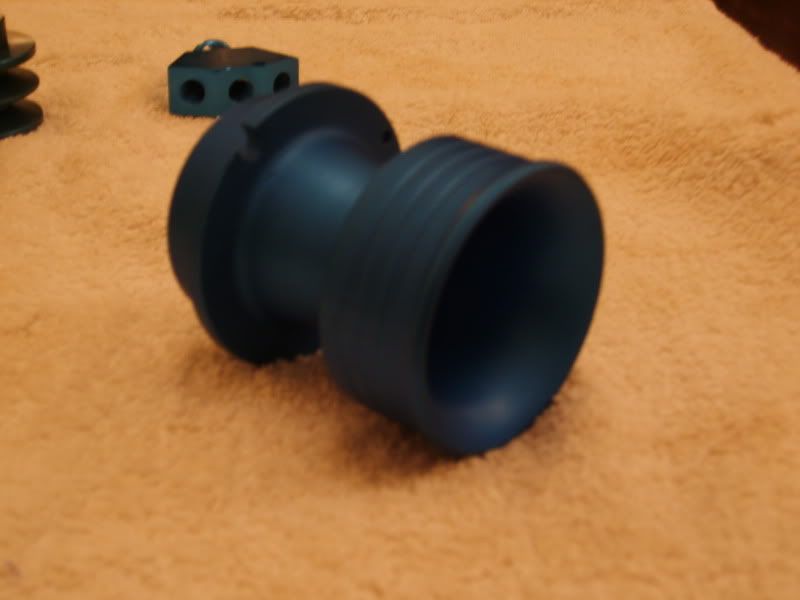
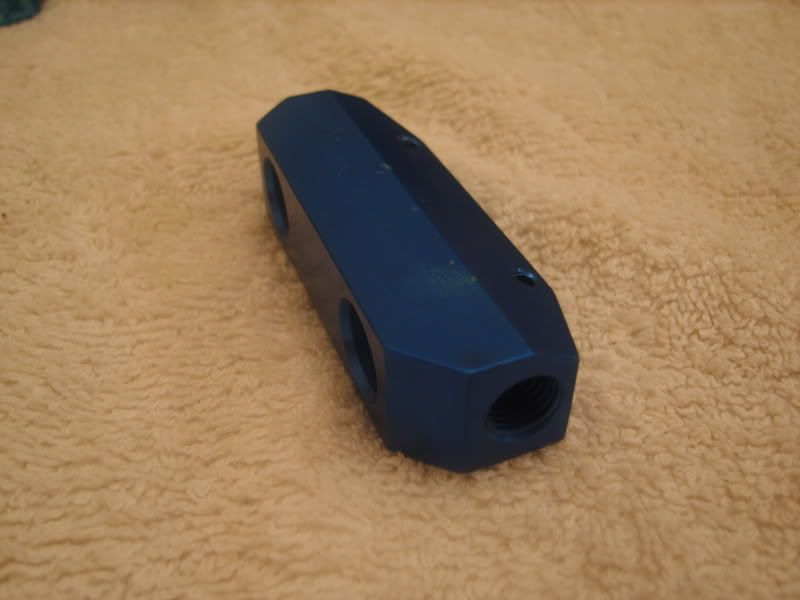
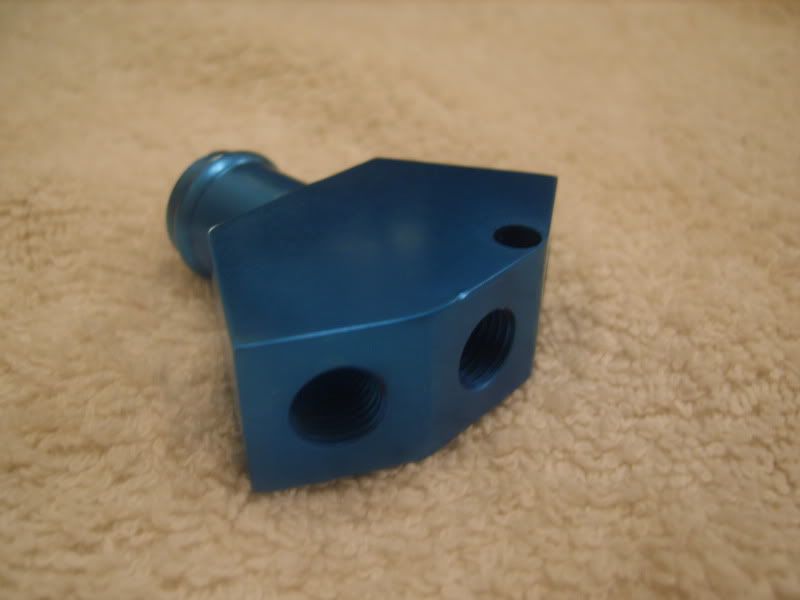
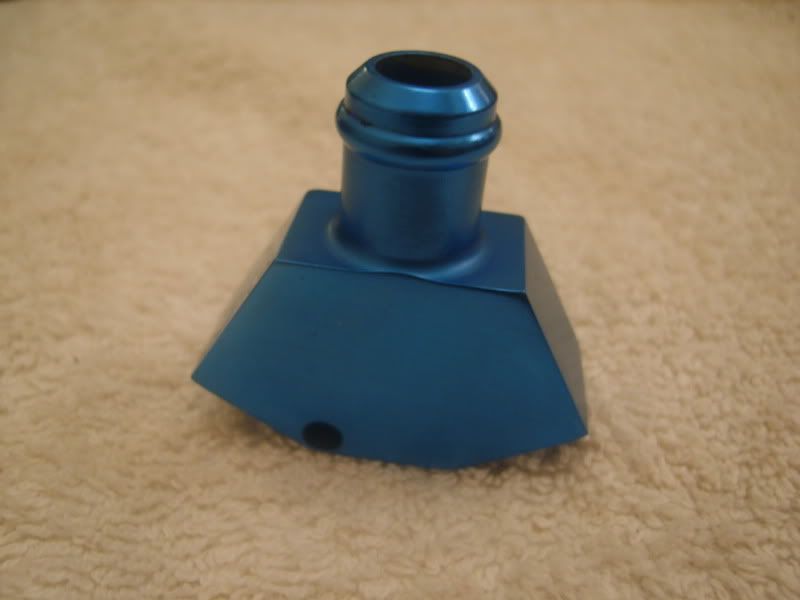
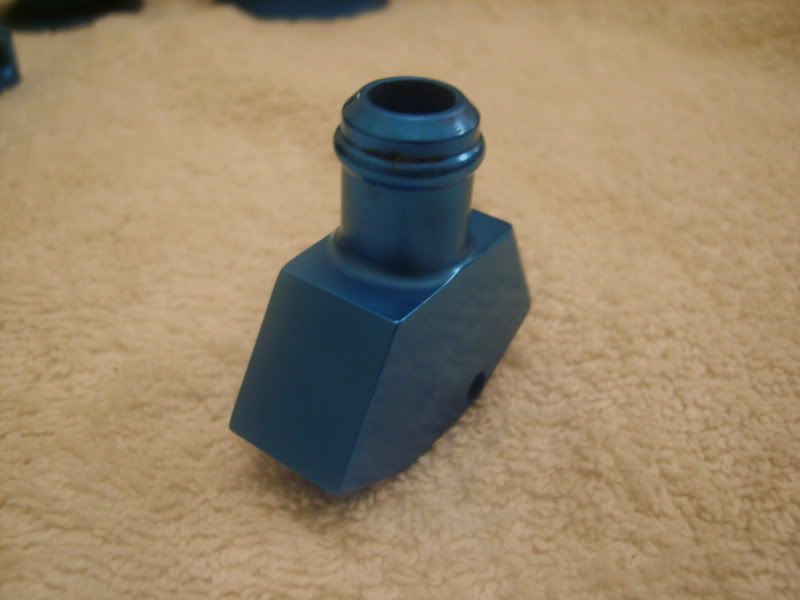
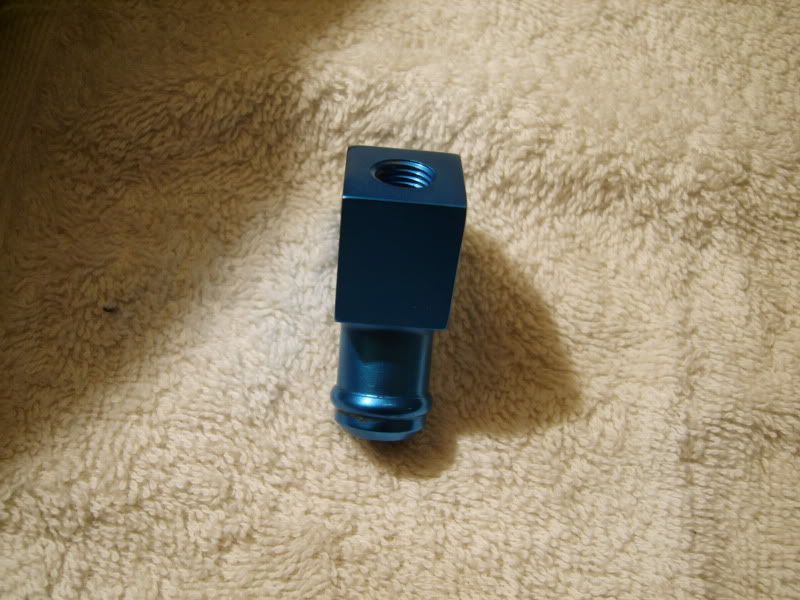
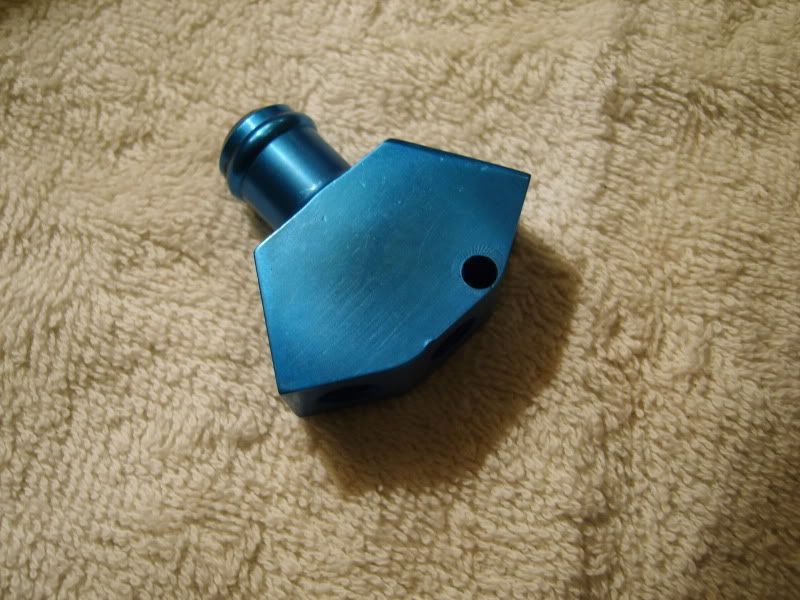
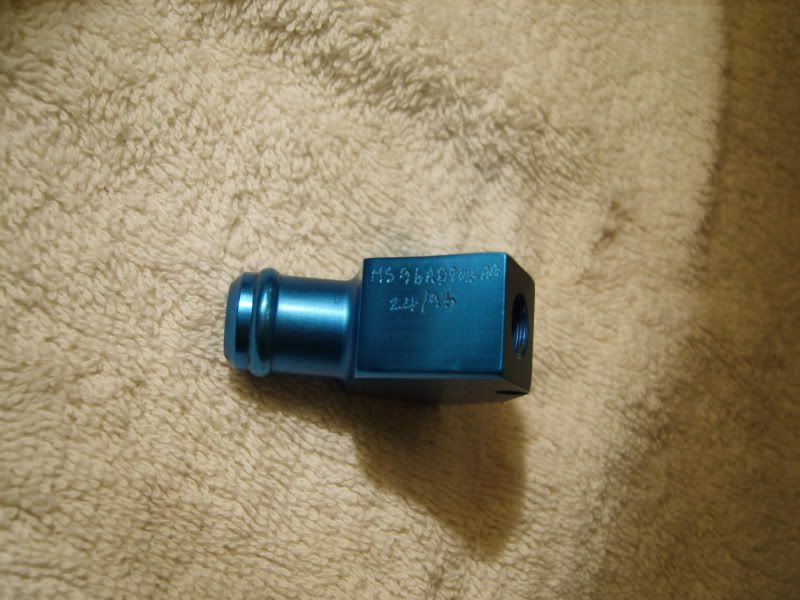
Only got blue dye at the minute but I have some gold and red arriving this week...
Some of the parts need to go back in, but overall i'm quite pleased...
Ian
Comment